Real-Time Manufacturing Traceability
- Çağkan Ekici
- Nov 15, 2021
- 2 min read
Updated: Nov 15, 2023
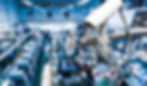
Traceability is fast becoming an important part of the manufacturing process for companies in diverse industries. Considering the significant cost, resource and productivity advantages it provides, it is not hard to see why.
Companies can control their production process by implementing solutions that encourage high-level tracking, assisting and reporting capabilities. This helps them make safer, more efficient, and higher quality products and create processes that can be optimized for continuous improvement.
Traceability is the ability to track every part and product throughout the manufacturing process. The word Traceability combines ''Trace'' and ''Ability'', which means the solution that enables high quality and safer manufacturing.

Importance of Traceability in Manufacturing
Having a good traceability system helps the manufacturer to improve quality, reduce costs, optimize processes and ultimately reduce issues and defects throughout the production process.
Here are the top five reasons why manufacturing operations need traceability:
1. Root cause analysis
Having access to all the data on products' steps enables in-depth review to determine the source of a problem and perform a root cause analysis. Performing these analyzes can help to prevent errors and improve any underperforming areas in the production processes.
For example, if your products have an error at any production line step, a root cause analysis determines which part of the production line caused the error. Since Traceability involves gathering information about each step of a manufacturing process, it makes performing the analysis much more effortless.
By tracking parts and products through the manufacturing process, it can be monitored and detected problem areas and bottlenecks. The data provided by the traceability solution also can be used to identify and correct previously undetected issues in the production process.
Identifying points in the process where quality checks are required can result in early error detection. The earlier an error can be identified the cost to the manufacturer.
4. Gain better value
Through traceability, companies learn more about their manufacturing process. With this information, they can find ways to redesign the process and make it more efficient. By closely examining your operation steps and the time it takes to complete each production step, you can identify ways to gain better value from your resources.
5. It’s an obligation!
Finally, many manufacturing industries operate under government regulations. In fact, each year manufacturers spend around $190 billion to comply with economic, environmental, and workplace safety regulations as well as regulatory compliance taxes, according to The Manufacturing Institute. If this is the case for your organization, it may be a legal requirement for you to implement traceability.
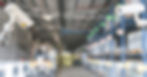
Improving Traceability in Production Lines with Khenda
Khenda is the first tool for truly gathering critical data from the manual production lines using AI-based video analytics. Our solutions allow you to monitor the entire production process and product life cycle, monitoring all required variables in real time and identifying errors as soon as they appear.
Our customers simply upload a video of the production that they want to analyze. Khenda automatically gathers cycle time data of each process. It brings high visibility to your production and offers you real-time awareness.
Tracing your production process will help reduce issues and errors, resulting in lower costs and a less frequent need for product recalls.
Get in touch with our team for more information.
References