Ultimate Positive Impacts of AI on the Manufacturing Workforce
- Çağkan Ekici
- Apr 25, 2023
- 4 min read
The manufacturing industry has undergone numerous transformations over the years, with the introduction of new technologies being one of the most significant drivers of change. Artificial intelligence (AI) is the latest technology that is set to revolutionize the manufacturing industry. By automating monotonous, repetitive tasks and augmenting human decision-making, AI can have a profound and positive impact on the manufacturing workforce. In this blog, we will explore how AI can positively impact the manufacturing workforce.
The Need for AI in Manufacturing
Manufacturing companies are increasingly turning to AI to address their capability challenges and talent shortages. The most significant advantage of using AI in manufacturing is that it allows businesses to automate monotonous, repetitive tasks, freeing up the workforce to focus on other more value-adding activities. According to a survey by OECD, in manufacturing AI technology is most commonly used in production processes (60%) and maintenance tasks (40%).
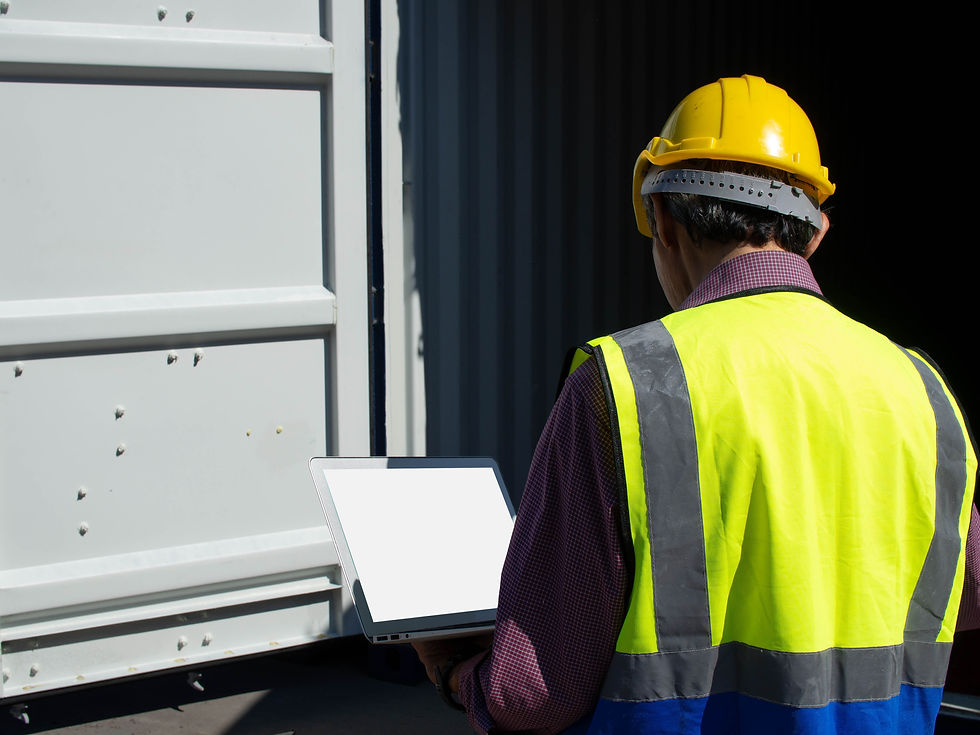
Upskilling the workforce with AI
As AI continues to transform the manufacturing industry, the workforce must also adapt to the new reality. While many may assume that AI adoption requires workers skilled in programming and data science, there is a need for critical thinkers and problem-solvers as well.
Investing in upskilling programs is crucial to ensure a smooth integration of AI into manufacturing processes. This will also help develop the talent that manufacturers already have. As Manufacturing Institute Vice President of Workforce Solutions Gardner Carrick mentioned during the “Manufacturing Leadership Council’s Manufacturing in 2030 Project: Let’s Talk about AI” event, AI improves the job quality of individuals on the shop floor. It provides better tools, and greater authority, and ultimately increases the value-add of their jobs.
Building partnerships with local schools, community colleges, and technical and vocational schools to develop talent pipelines can also help meet the needs of the future. This will not only benefit manufacturers but also help the workforce adapt to the new reality of AI.
Combining human and AI collaboration
AI is not meant to replace humans in the manufacturing workforce. Instead, it is designed to augment and support employees in their daily work. “While AI can handle monotonous, repetitive tasks; human labor will still center around making decisions and telling stories”, according to Asi Klein, Managing director of Industrial Products and Organization Transformation at Deloitte Consulting.
In the manufacturing industry, AI can assist in decision-making processes and collaborate with humans to design new products or systems. This can be particularly useful in optimizing supply chain management and improving communication and collaboration across different disciplines. An OECD survey found that more than 50% of manufacturing companies are using AI to improve worker performance.
Employers say that improving worker performance is one of the main motivations for adopting AI
% of employers that have adopted AI
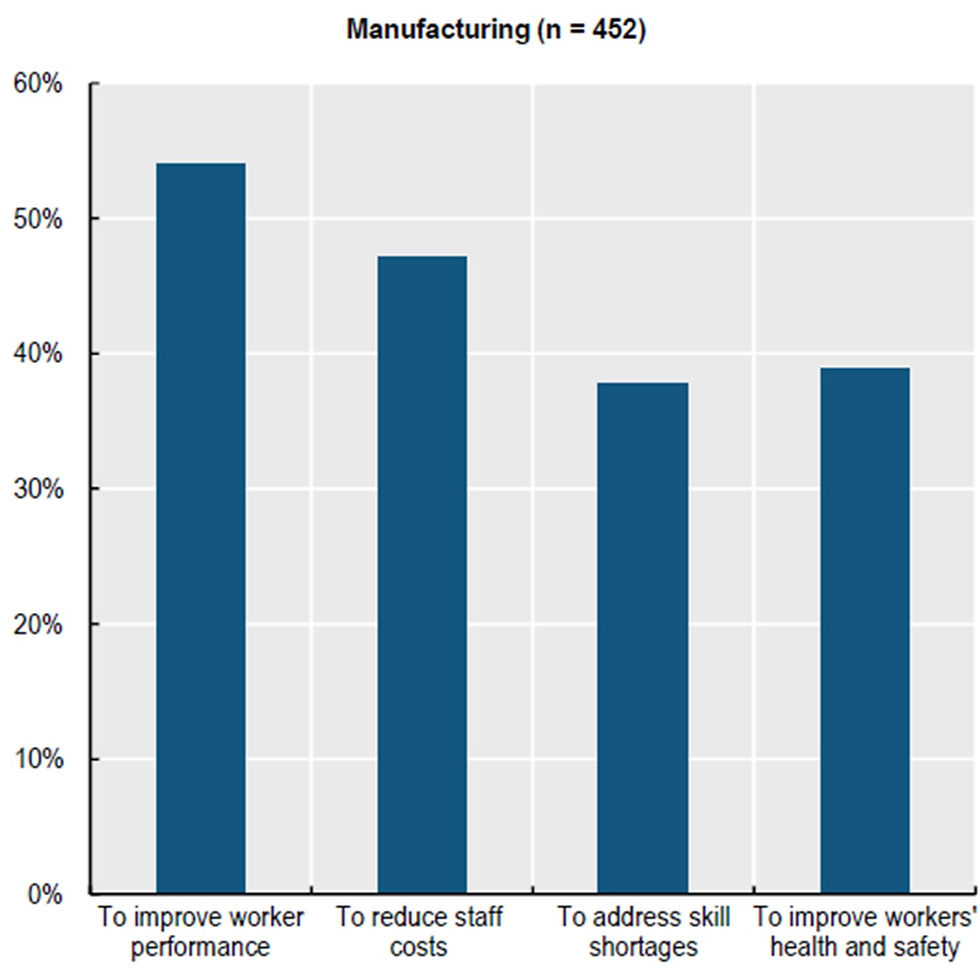
*Source: The impact of AI on the workplace: Main findings from the OECD AI surveys of employers and workers, 2023
Scaling AI in manufacturing
Scaling AI in manufacturing has been a challenge for many manufacturers due to various factors, including a lack of AI capabilities and skills, limited availability, quality, or use of data, and a missing overarching strategy. However, as AI becomes more integrated into manufacturing processes, it is essential to scale effective AI pilot applications to fully benefit from their impact.
According to a report by OECD, employers are most positive about the impact of AI on worker productivity in their company. The positive reported impact on worker productivity is encouraging given that the most commonly reported motivation for adopting AI was to improve worker performance.
The positive attitude of employers toward adopting AI in the manufacturing industry is crucial. Manufacturers need to adopt a comprehensive approach to AI implementation, including developing a clear strategy, establishing a governance structure, investing in talent and resources, and prioritizing use cases that align with business goals.
Employers that have adopted AI are positive about its impact on worker productivity and working conditions
% of employers that have adopted AI

*Source: The impact of AI on the workplace: Main findings from the OECD AI surveys of employers and workers, 2023
Conclusion
AI is transforming the manufacturing industry, and its impact on the workforce is both significant and positive. AI can help automate monotonous, repetitive tasks, freeing up the workforce to focus on more value-adding activities. It can also augment and support employees in decision-making processes and human-robot collaboration. However, scaling AI in manufacturing has been a challenge, and manufacturers need to adopt a comprehensive approach to AI implementation to fully benefit from its impact.
As manufacturers continue to embrace AI, upskilling the workforce will be essential to ensure a smooth integration of AI into manufacturing processes.
AI is not meant to replace humans in the manufacturing industry. Instead, it is designed to augment and support the workforce. Manufacturers need to embrace AI as a tool to improve efficiency, increase productivity, and reduce costs while ensuring that the workforce adapts to the new reality of AI.
Khenda’s AI-based platform and video analytics help bridge the gap between manual operations and digitization. Advanced analytics allow engineers to transform continuous improvement, and understand productivity metrics to ensure operational excellence. With Khenda, every engineering team can achieve operational excellence.